CUSTOMERS
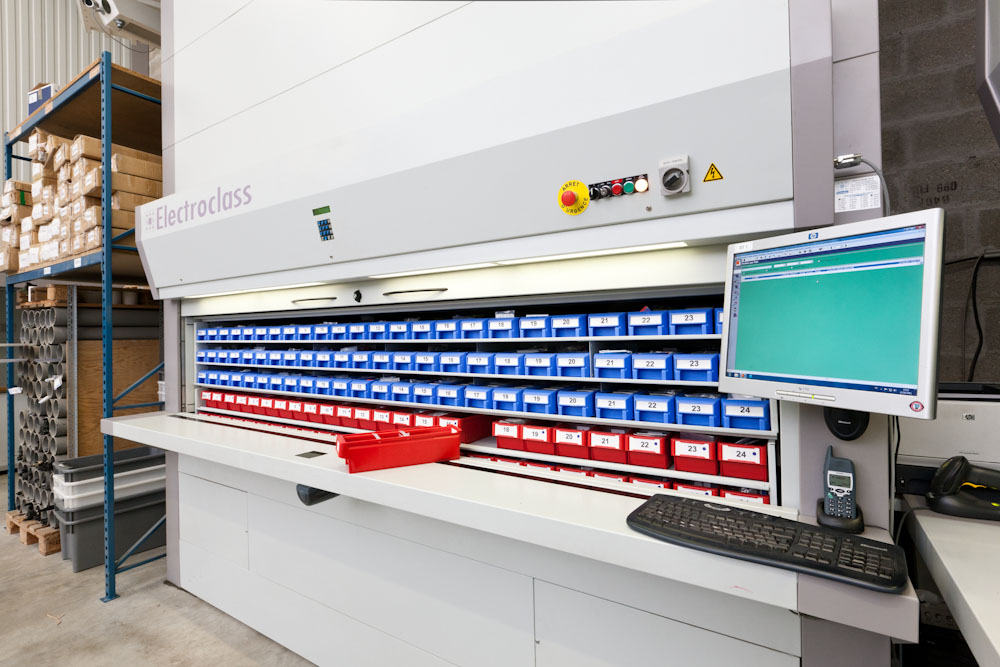
17 October 2018
Customer Presentation and Needs
Model Racing Car, key player on the high-end scale-model market draws on a network of specialized boutiques which target a demanding clientele comprising enthusiasts and connoisseurs. MRC's success is based on the outstanding quality of its products as well as its services. In 2006, Patrick Rigot decided to invest in an automated storage solution and to interface his stock management with his SAGE commercial management software.
MRC's central warehouse comprises highly-heterogeneous stock: over 100 models of finished products, of every size, and some 11,000 references of spare parts in every price range. The parts contained in the stock are of various volume sizes from a few cm3 to 1 m3. Over 10,000 components and parts which MRC needs to manage for its customers. For both finished products and spare parts, MRC proposes delivery within 24 hours once the order is confirmed. A simple shipping error may quickly lead to significant operating losses.
An optimal storage solution for each product family
To work out the best solution, ELECTROCLASS studied the profile of the product families: volume, quantity, ABC analysis, etc. Spare parts which require various yet fast picking are stored in TITAN carousel storers set up with special containers whilst finished products, which are shifted less, are stored in mini SILO ASRS.
These two machines are replenished with packages receive from suppliers. They play a dual storage role as they are compact and distinguish precisely between products so picking is faster and efficient (pick-to-light is particularly important for small parts). Disparate references are stored in the JUMPER storage tower, which can also store small-parts packages before they are distributed to the TITAN vertical storers.
A solution which is fully managed and operated by G-STOCK WMS.
When stock are input, G-STOCK automatically assigns the most appropriate space taking into account volume and the quantity of parts to be stored.
"G-STOCK offers user-friendly ergonomics making it easier for our warehouse/store staff to use. It only takes 15 minutes to train someone up on it."
As regards output, the management software operates the automated storers simultaneously by optimizing picking movements. As soon as one line is validated by the operator on one of the storage machines, the operator then receives the instruction to move on to the following reference.
Once picking is finished, the order is moved to the packaging/shipping department on a transport trolley.
"This set-up ensures the work can be done as hidden time, an important vector for the high number of lines to be dealt with per hour. We are able to ship over 100 orders with an average of 10 lines per order. With only 1 warehouse/store employee, we successfully deliver within 24 hours even though the numbers of orders and our references have greatly increased."
Benefits for MRC:
This solution enables us to complete a 10-line order in less than 4 minutes. Patrick Rigot goes on to add: "even if, in theory, zero fault doesn't exist, we haven't come across any stock difference when doing our end-of-year inventory, or any shipping error. Our quality-of-service targets are attained."
"Thank goodness we met and were able to work closely with ELECTROCLASS, otherwise we would have missed out on making five figure and even six figure operational savings. This solution currently ensures we outperform all our rivals and, well, it would have been a real shame to have let others take pride of place. Fortunately we are, and we're going to stay a gigantic step ahead. "
Comments made by Patrick RIGOT, founder and CEO of Model Racing Car