CUSTOMERS
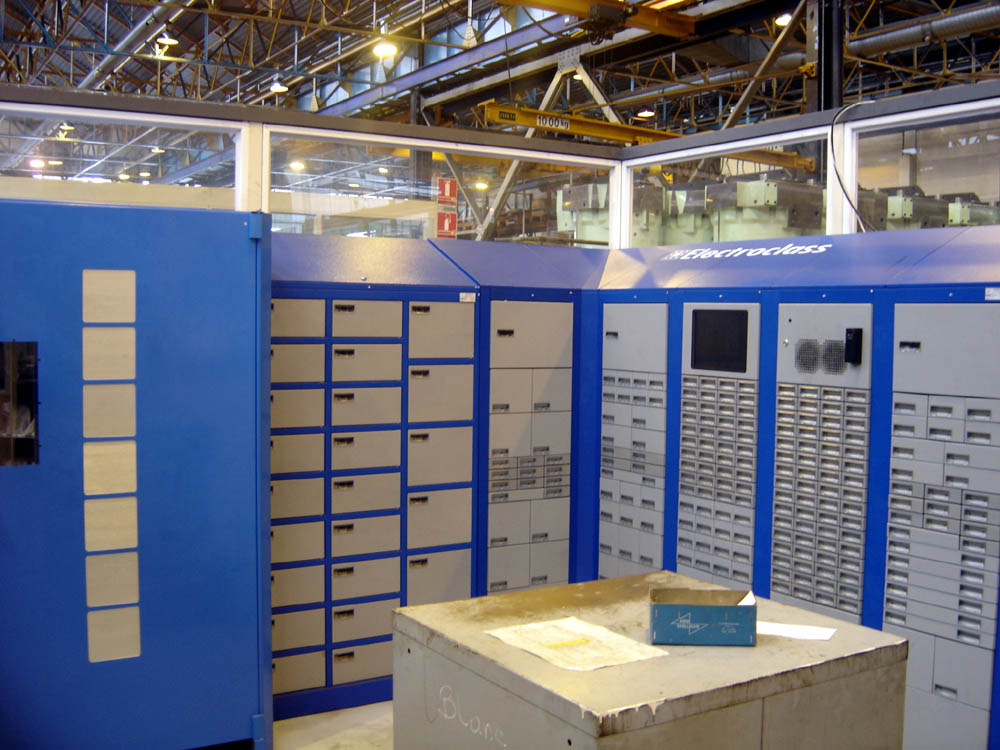
18 October 2018
Customer Presentation and Needs
Equipment was stored and distributed in a traditional way using key-locked drawer cabinets prior to vending machine installation. Each workstation had its own buffer stock as each operator created their own stock independently. Operators would fill in a consumption declaration specifying the product reference as well as the quantity taken.
"We have a distorted overall perspective and really bad tool stock control (…) as, for example, we could actually go ahead and order parts without knowing if they were still in stock or not or if they were part of buffer stock at machine level."
ELECTROCLASS all-in solution
"We wanted to choose a specialized supplier yet ensure we would continue to have maximum flexibility as regards equipment configuration: ELETROCLASS met both these aspects"
The SupplyPoint set up initially was able to manage 169 references (value of 125 K€) for some 32,000 units consumed and 2,700 outputs per year. The additional investment made subsequently led to setting up 5 LockerPoint cabinets and a RotoPoint vending machine and targeted 127 other references (value of 145 K€) for 28,000 units consumed over a year. One piece of software installed on a central mainframe computer manages all the equipment.
Today, around 200 people use the ELECTROCLASS solutions: machine operators, machiners and assemblers who need to take equipment from the vending machines. By presenting their badge, users access a scroll-down menu proposing the tools or PPE related to their job.
"Set-up was carried out in record time: the SupplyPoint vending machine was integrated and operational in less than three months and, as for the RotoPoint, it only took a few days to integrate it"
Project results
This approach led to ensuring perfect operation tracking and to creating separate statistics, listed by machine, by activity sector and by production cell.
"Thanks to SupplyPoint and RotoPoint, we were able to manage everything, to control everything and to track all operations from a single place, with an overall emphasis on making savings."
Mr CUARTERO also declared that the ELCTROCLASS installation had made it much easier to manage consumable stock and had improved operators' daily working conditions. Moreover, when staff take days off, the system is programmed to remain 24/7 operational and, at the same time, to be able to autonomously supply equipment for 15 days.
"With less than 2 years' amortization, annual savings of around 60 K€, (…) the cost of the solution has been totally recouped, knowing that our annual tooling operating budget was reduced by 25% compared to the last 2 years prior to the installation"
Comments made by Mr Raphaël CUARTERO, Head of Industrial Engineering & Maintenance
Man Diesel & Turbo Customer Application Sheet