Customer applications
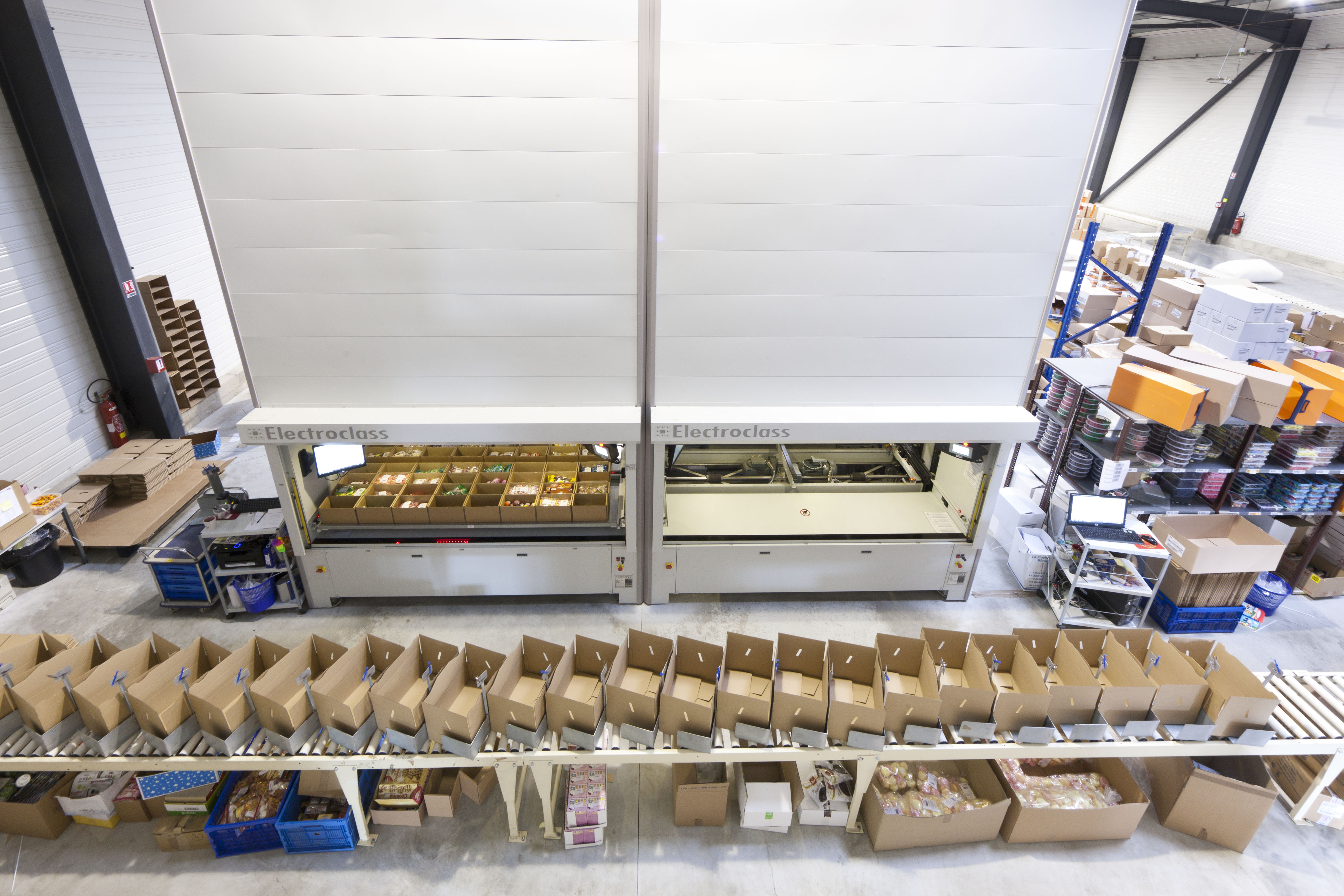
02 October 2018
Customer Presentation and Needs
Originally, HORIZON 2000 had an undersized building for storing its received goods and for order picking. Received goods were stored on racking systems which meant that order pickers had to move and manually pick the products based on information transmitted to them orally. The conveyor system used for order picking was relegated to a cramped space.
"The main issue was trying to store all our ranges of sweets and confectionery in their respective storage spaces, then to find them easily, using tailored FIFO management and to be able to manage the use-by dates."
This lack of optimization and tracking led to a significant number of errors in orders involving losses which were sometimes considerable. Given these issues, HORIZON 2000 management wanted to find a storage solution quickly which would be tailored to their issues and would in particular enable them to:
- Deal with their growing business by optimizing storage spaces,
- Improve customer satisfaction by making order picking more reliable,
- Increase productivity by improving stock control and by limiting the number of operators,
- Save time when processing orders.
"ELECTROCLASS won us over because it presented a comprehensive all-in solution integrating equipment and software with a single supplier-contact project manager. The project was implemented over 3 months, a real challenge which ELECTROCLASS brilliantly met by totally complying with lead times for both the equipment side and the software side. And all this accompanied by a customer support team which was incredibly available."
ELECTROCLASS proposed to set up two 7-metre high storage towers each with double front/rear access. One side for storing goods received and the other dedicated to order picking and preparation. As such, two teams (reception / order picking) can work perfectly at the same time in a totally separate manner on the same storage towers. Each of these towers contains drawers specifically designed for various product sizes and packaging.
"The ELECTROCLASS solution enables us to manage extremely high order flows with only one operator working who can process up to 25 orders at
G-STOCK management software, published by Electroclass, controls these storage towers. The use of a barcode reader scanning goods received and order picking optimizes time. G-STOCK WMS is interfaced with the commercial management software which HORIZON 2000 uses.
"Productivity gains, reductions in order errors, enhanced customer relationships, customers are more satisfied, use-by dates are better managed, classification by product area is better identified. (…) If ever we were to start all over again, we would definitely choose the same solution without any doubt."
Comments made by Mr Sébastien WALTENER, HORIZON 2000 co-CEO.